Supply chain management processes combine planning, sourcing, procurement, production operations, distribution, and organizing, all under effective day-to-day operations, including document management, logistics, transportation, and more. We also see the impact of the last stage in SCM, which is aftermarket.
Today, businesses should be aware of what impacts their daily activities. This awareness of supply chain complexities can help draw more adequate conclusions regarding efficiency and the ease of continuous improvement, as well as supply chain resilience.
These results are visible with the invention and deployment of technology and customer software development, which, according to McKinsey, has major potential. In 2023 alone, companies noticed a shift from 37% to 79% in investing in modernizing supply chains. Thus, technology in SCM is a driver of resilience, which aligns with benefits for the entire industry, such as cost-effectiveness and lower resource usage.
What is supply chain management?
Supply chain management is a set of tasks and responsibilities that need to be arranged to effectively deliver goods from producers and manufacturers to the end customer. Along the way, several activities and tasks need to be performed to store goods, distribute them, and transport them.
According to McKinsey, seven types of supply chain stakeholders completely overlap with our experiences and cover several crucial activities in the supply chain that we have mapped in this article.
Here are seven types of supply chain stakeholders based on McKinsey research:
Producers: those who grow or produce raw materials for goods.
Vendors: those individuals or companies involved in buying and selling materials
Manufacturers: those responsible for transforming materials into finished goods
Carriers or logistics providers: those involved in transporting goods around the world.
Supply chain managers: ensure smooth operations, from sourcing raw materials to production, delivery, and returns.
Retailers: companies that sell goods through online platforms or physical stores.
Consumers: individuals who buy and use goods and services.
What are the most important supply chain management tasks?
Supply chain management tasks encompass all operations that combine crucial elements of today's logistics and transportation, which are closely linked to manufacturing. Certain activities, from production plants to delivering goods to the final customer, are based on SCM tasks. We can also see what the flows in the supply chain may look like:
Production: Developing strategies to effectively meet customer needs and minimize costs.
Sourcing: Selecting and managing suppliers to acquire materials and services.
Manufacturing: Transforming raw materials into finished products.
Distribution: Effectively moving products from production to customers and inventory management.
Operations: Managing the day-to-day operations of the supply chain.
Aftermarket: Providing after-sales support and services to customers.
We observe that tasks in supply chain management involve effective planning, where supply chain strategy is key to streamlining further processes. We perceive this element as the most important in developing further actions towards effective settlement of supply chain management activities.
Need help with supply chain software development?
Learn how we can boost your business processes
Explore moreEffective planning can be visible through evaluating supply chain challenges and reliably assessing risks and opportunities. This gives a foundation for other SCM activities, where we consider this in the context of specific areas where and what processes should integrate into our supply chain. We'll explain more about it in the next headline.
Moreover, according to Gartner, another factor in SCM planning is sales & operations planning (S&OP). The latest Gartner survey indicates that 64% of organizations anticipate customers' unexpected demand variation to increase over the next five years.
Figures from Gartner give us a clear hint that effective supply chain planning and strategy development for supply chains can help us become more resilient. At the same time, we can expect over 50% fluctuations in changing demand in the upcoming years.
Nevertheless, several more elements complete the supply chain management activities landscape and, to the same extent, help us understand what supply chain management tasks are.
Top 6 elements of supply chain management activities
We explored supply chain management activities and found that we could list six elements that facilitated further activities for all supply chain services. One way or another, we found these common areas crucial for supply chain development. This thesis was also confirmed among EMEA logistics managers involved in international operations.
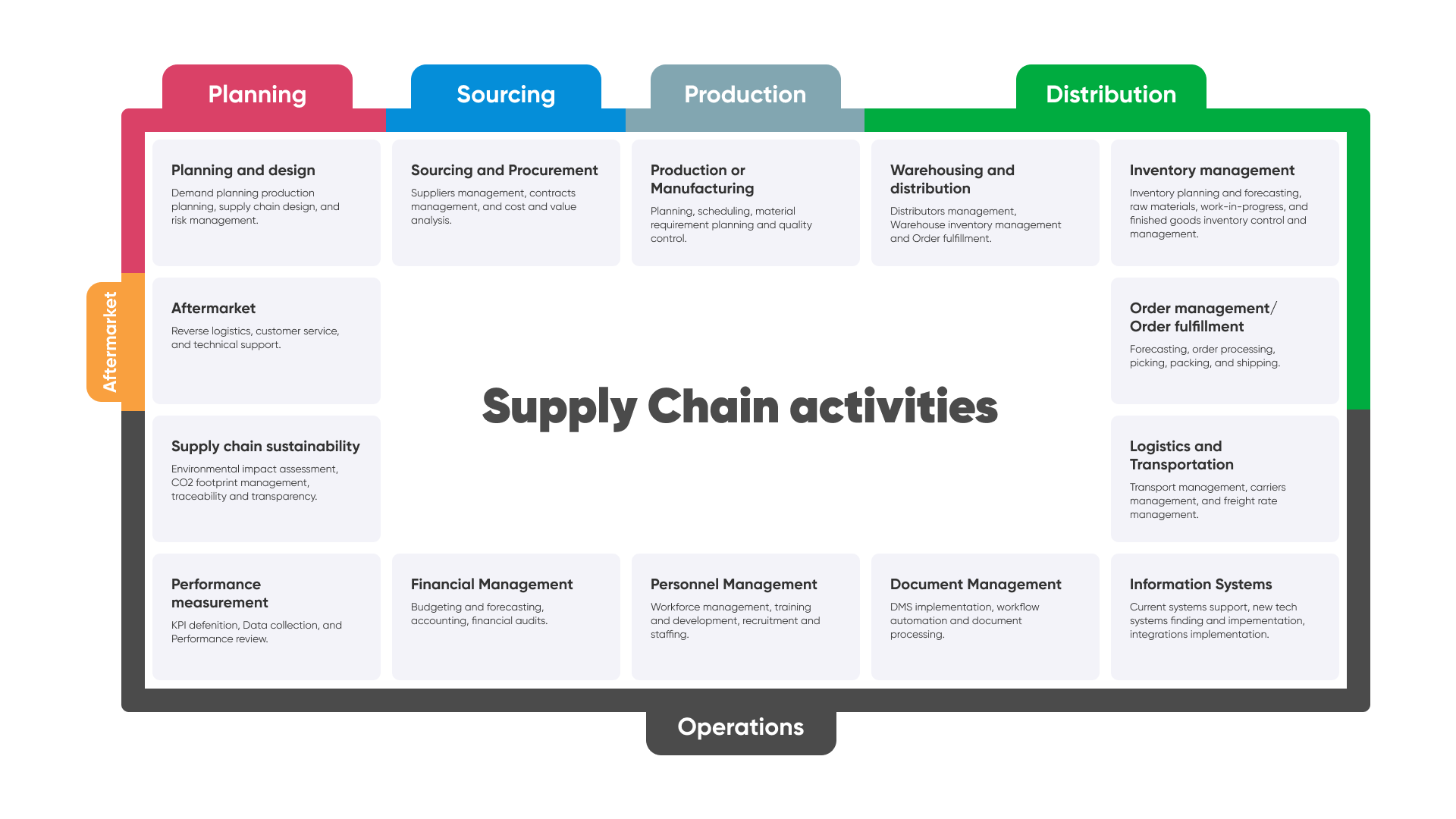
"A logistics company can help meet customer demands by providing efficient and effective transportation and delivery of goods, as well as providing reliable and timely information about the status of those goods. From a broad perspective of industrial classification, there are several ways in which a logistics company can support businesses in meeting precise customer needs (…)."
Burak Emre GÜNAY, Logistics Manager
1. Planning
Planning is one of the elements that composes the complete picture of the entire supply chain landscape and allows the outline of further actions that are taken to fulfill supply chain services. In the phase of planning, we think that Design and planning are crucial in shaping the entire network in SCM.
Let's take a look at this through our experience by working on projects such as developing truck owner's assistance applications. This project is live proof that understanding the value of design and planning with a handful of knowledge about SCM activities can help businesses from transportation and logistics build great solutions on projects where our team has had hands-on the project.
To some extent, the design phase includes requirements analysis. The process begins with a thorough understanding of the SCM system's characteristic needs and obstacles, which is the first step in the planning phase. This stage includes gathering requirements from stakeholders in various departments.
Once the requirements are understood, the next step is creating a solution tailored to the SCM environment. This phase includes creating the architecture, workflow diagrams, and implementation strategy.
Need help with custom mobile app development?
Learn how we can boost your logistic business processes
Explore more2. Sourcing
Sourcing is another crucial element when planning third-party logistics parties in the SC network. Companies use procurement platforms to outsource their contract logistics services that offer the best lower fees for distribution, transportation, or other services. We can find carriers, freight forwarders, IT companies that develop custom supply chain software solutions, and many others among those many businesses that are involved.
Sourcing involves identifying and selecting suppliers based on criteria such as quality, cost, reliability, and green and sustainable practices. Once suppliers are selected, the next step in sourcing involves the actual purchase of goods and services. This phase involves negotiating contracts and managing supplier relationships.
3. Production
This phase is crucial as it is where everything starts. So, from the starting point in SCM activities, we can say that this is the production stage or, however one wants to call it, manufacturing. SCM activities can partially cover here planning for delivering raw materials and further contract manufacturers, shipping to distribution centers, or in some cases, reverse logistics, where goods are moved back to production plants for recovery or utilization.
Operations in production and manufacturing involve demand forecasting and inventory management planning, where SCM can be responsible for processes such as Just-in-Time (JIT), Just-in-Sequence (JIS), or First-in, First-out (FIFO). Supply chain operations also include lean manufacturing processes, quality management, and supplier collaboration.
4. Distribution
We have a very important element of activities in supply chain operations here, which involves the journey from the purchase order, something in e-commerce online stores, to the customer's house or other centers in the warehouse in B2B.
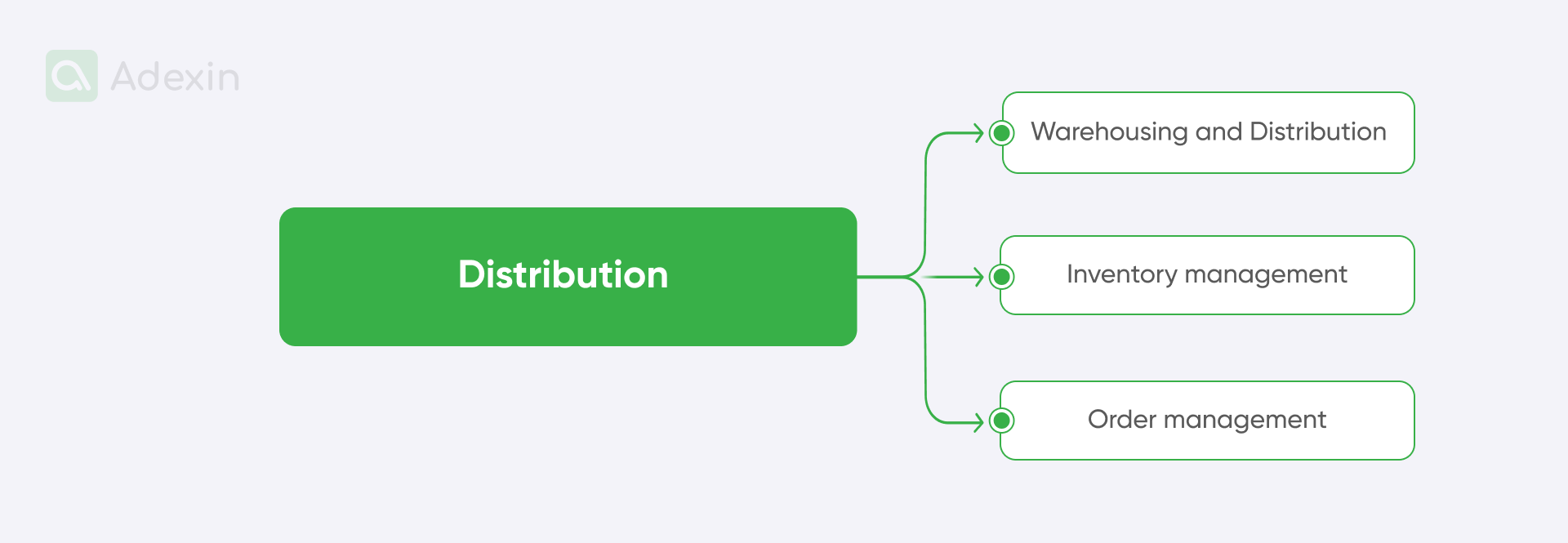
We have outlined three parts:
Warehousing and Distribution. Warehousing and distribution are key SCM functions involving storage. They involve the movement and delivery of goods. The warehouse function plays a role in inventory management and facilitates efficient logistics operations.
Inventory management. Inventory management is necessary in SCM to optimize inventory levels to meet customer demand while minimizing costs. It includes monitoring, controlling, and replenishing inventory to ensure efficient supply chain operations.
Order management/order fulfillment. Order management and fulfillment focus on processing and delivering customer orders in an exact and timely manner. These stages include purchase orders, processing, and fulfilling customer orders. Behind this process is standing technology to streamline processes and improve customer satisfaction.
5. Operations
Operations in SCM is a widespread term. It covers so many little parts of the business, but I would like to focus on those that are very impairing the continuous well-functioning of CM.
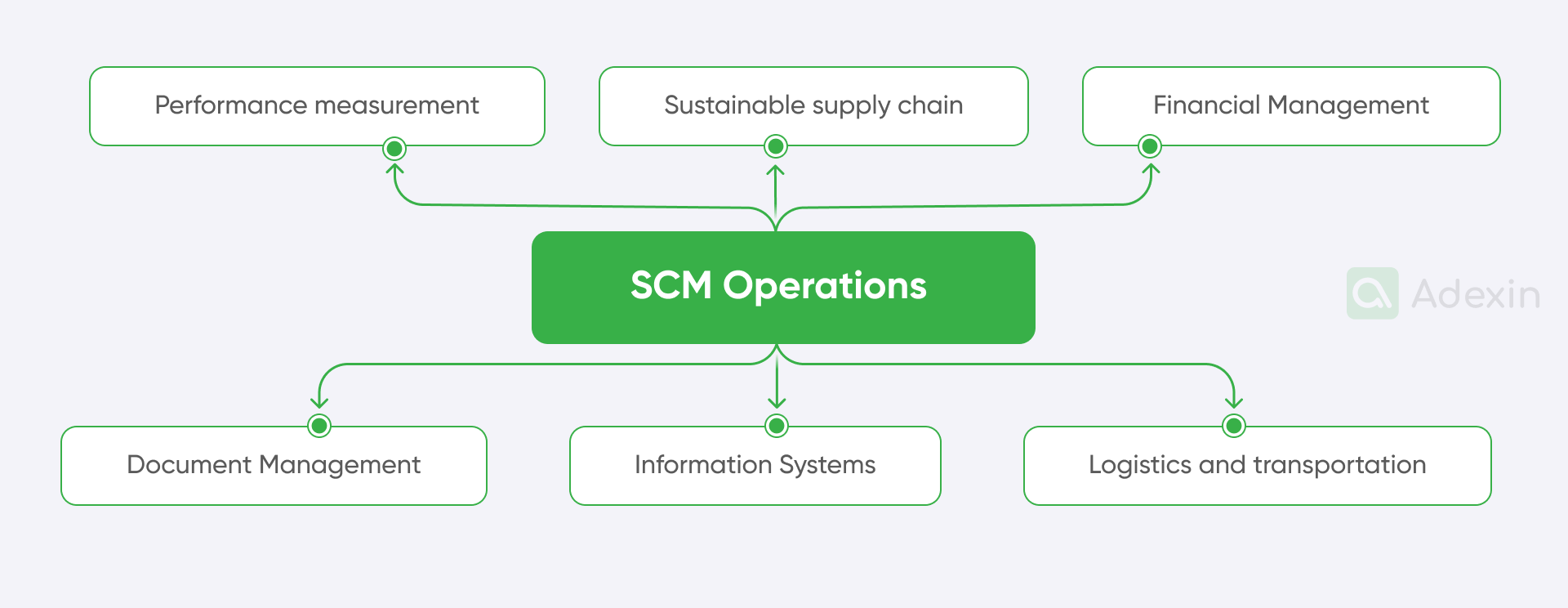
To some extent, our outcomes match the Supply Chain 4.0 concept, which is embraced by McKinsey, where there is no future without technology and agility in SCM:
Sustainable supply chain. A sustainable supply chain focuses on environmentally, socially, and economically sustainable practices. Simply put, it includes reducing environmental impact while promoting ethical labor practices and ethical sourcing.
Performance measurement. Evaluate supply chain efficiency and performance using key performance indicators (KPIs) such as cost, quality, delivery time, and customer satisfaction. These indicators are most important for identifying areas for improvement and optimizing performance.
Financial Management. Manages financial resources and costs associated with supply chain operations, including budgeting, cost control, pricing strategies, and financial analysis to ensure profitability and viability.
Document Management. Organizes and manages documents and records generated by supply chain processes. DM is often enabled by a Document Management System (DMC) that facilitates efficient storage, retrieval, sharing, and compliance.
Information Systems. This area is about providing the technology infrastructure and tools to plan, execute, and monitor supply chain activities. It is often supported by custom software development, which enables real-time visibility, data analysis, collaboration, and automation.
Logistics and transportation. These two elements cover the movement of goods from suppliers to customers. They include transportation and route optimization, carrier selection, freight management, warehousing, and distribution to ensure timely delivery and cost efficiency.
6. Aftermarket
In supply chain management (SCM), the aftermarket refers to the market for goods and services sold after a product's initial sale. This is crucial as it must encompass external elements connected with marketing and sales activities to maintain the highest level of customer satisfaction and encourage repeat orders.
The aftermarket segment includes spare parts, repairs, maintenance services, and upgrades. Aftermarket SCM involves managing spare parts, service operations, reverse logistics, customer relations, and pricing to maximize revenue and customer satisfaction.
Are you in search of a reliable tech partner?
Adexin can help with advanced logistics solutions
Contact usFinal takeaway
From my experiences, we see that today's companies need to understand the complexity of their daily operations to draw the right conclusions about supply chain performance. Continuous improvement and resilience are very important and cannot be ignored when it comes to making plans and designs in the supply chain. Advanced technology plays a key role in improving SCM. Significant investments in supply chain modernization have already proved this and it's clear that high-tech is providing better visibility in SCM and better resource management.
To optimize supply chain management and streamline business operations, we can help you see how our end-to-end solutions can improve efficiency and resilience. Contact us today to learn more and start your journey toward supply chain excellence.